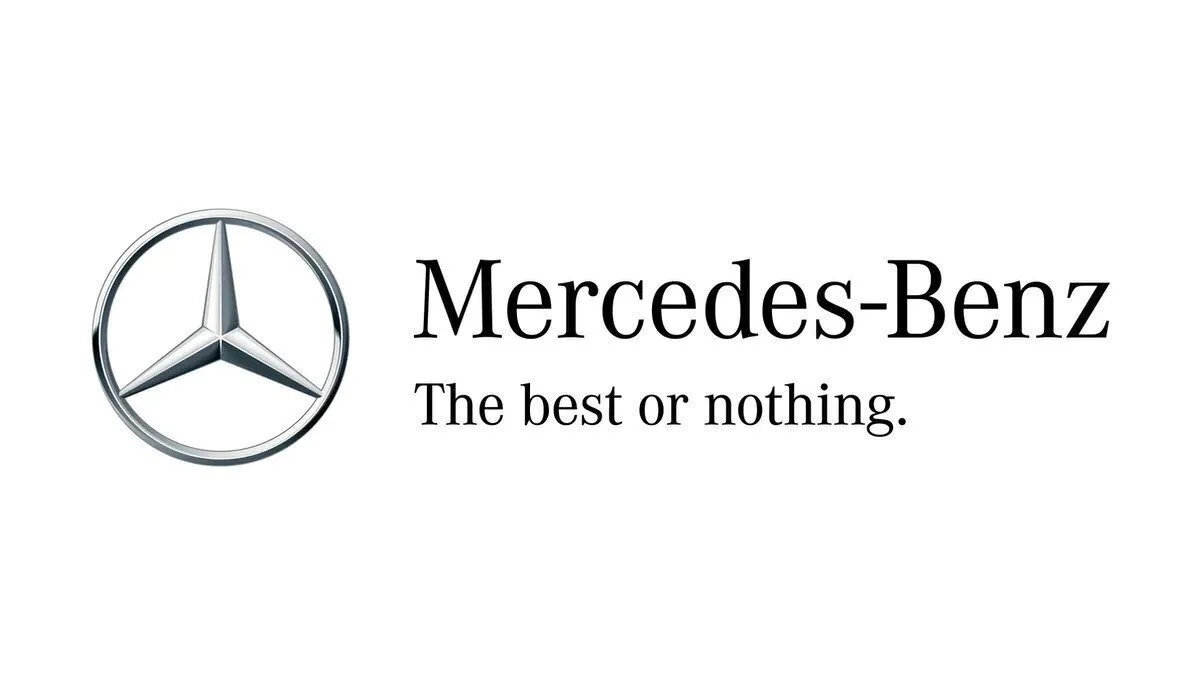
Engineering Intern - Jacksonville, FL
October 2019 - May 2020
The Mercedes-Benz Quality Evaluation Center in Jacksonville handles North American quality, parts testing, repair procedure testing, warranty claims, technical service, and parts distribution. In collaboration with the QEC’s Quality Management department, I was able to work on projects to enhance efficiency and help grow sources of useful data.
Quality Management’s main goal is to source and contextualize as much data as possible to provide actionable design and service suggestions.
Projects:
Vehicle Ingestion Macro Scripts
Description: When vehicles are received from production for distribution (at the Vehicle Preparation Center), they receive market specific additions, repair of damages sustained during transport, options install, and modification actions. Modifications range from software updates to major repairs in accordance with warranty compliance. It was not uncommon for vehicles to be in the auto show circuit for long periods of time, disallowing modifications to be performed. When these vehicles would return to the VPC (Vehicle Preparation Center) records on completed and necessary modifications would be scattered through a variety of platforms. After ingesting these vehicles manually for some time, I pitched the idea of automating the process to supervisors. After approval, I detailed, built, and distributed this tool.
Responsibilities:
Ingest completed and necessary vehicle modifications into SAP manually
Outline data sources, processing steps, and necessary output
Research and learn Windows scripting language and tools
Write custom scripts to pre-process vehicle VINs, and gather relevant data automatically (Using AutoHotkey and scripting language)
Package and distribute data ingestion tool using excel
Present process flow and usability to relevant parties
Accomplishments:
Increased vehicle modification ingestion by 82%
Note: time spent using this tool is also idle, instead of active user input
Automated and simplified future modification ingestion on potentially thousands of VINs
Paperless Pre-Delivery Inspection Platform
Description: To best ensure customers receive vehicles in the state they expect to receive them in cars must be inspected several times before delivery. The issue with the platform previously used was that live data was not reported, checklists were static, and accountability was questionable.
Responsibilities:
Project management
Build familiarity with the end user of both the data entry (technicians performing pre-delivery inspections) and data reporting (quality management)
Ensuring the needs of each party are satisfied to maximize project benefit
Research quality metrics to understand desired affect
Perform checks using old system
Assist in performing cost consolidation based on team cost vs benefit analysis
Revise app and back-end mock ups (using Adobe XD) to increase usability, decrease project costs, and increase ease of development
Prototype Microsoft Access/Sharepoint forms and databases for additional pre-delivery check items to be added
Collaborate with supervisors to communicate with development team
Clarify questions regarding features and functionality
Accomplishments:
Reduced project cost by over $90,000 through feature elimination and internal development
Related Skills
Data analysis
Data processing
Project management
Microsoft Excel
Microsoft Access
Macro scripting
Cost consolidation
Data contextualization